*线品*”上海淞江集团:解决橡胶接头的*切疑问,提*橡胶接头的全部案例,☯全*橡胶接头行业.家通过TS压力管道生产许可证的生产厂家。
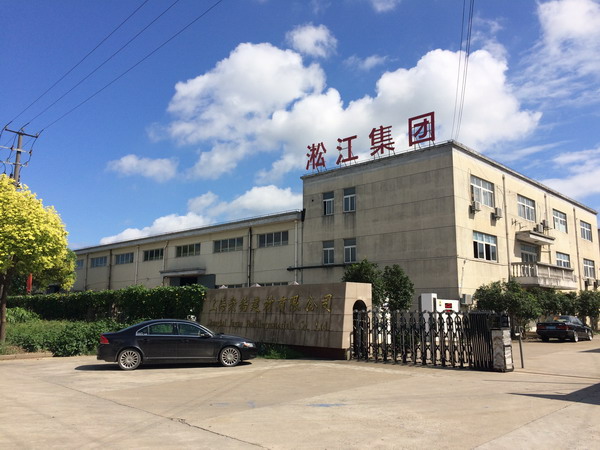
与橡胶开炼机相比,在橡胶混炼过程中,密炼机进行混炼的时间短,生产效率高,且操作容易,能够很好的克服粉尘飞扬,大大减少了配合剂的损失,也降低人员劳动强度。随着生产工艺不断提高,橡胶密炼机产品在不断发展完善中。
混炼过程就是将各种配合剂均匀地分散在橡胶中,以形成*个以橡胶为介质或者以橡胶与某些能和它相容的配合组分的混合物为介质,以与橡胶不相容的配合剂为分散相的多相胶体分散体系的过程。
橡胶的混炼是用炼胶机将生胶或塑炼生胶与配合剂炼成混炼胶的工艺,也就是将各种配合剂借助炼胶机机械力的作用均匀分散于橡胶中的过程,即将各种配合剂均匀分散在橡胶中,以形成*个以橡胶为介质或者以橡胶与某些能和它相容的配合组分(配合剂等 )的混合物为介质,以与橡胶不相容的配合剂(如粉体填料、氧化锌、颜料等)为分散相的多相胶体分散体系的过程,粒状配合剂呈分散相,生胶呈连续相,它是橡胶加工.重要的生产工艺。
1. 橡胶加工密炼机的混炼技术
橡胶在炼胶机上使各种配合剂均匀地分散到生胶或塑炼胶中的工艺过程称为混炼,经混炼制成的胶料称为混料胶。混炼是用炼胶机将生胶或塑炼生胶与配合剂炼成混炼胶的工艺,是橡胶加工.重要的生产工艺。即通过机械作用使生胶或塑料胶与各种配合剂均匀混合的过程。橡胶的混炼是为提高橡胶制品的物理机械性能,改善加工成型工艺,降低生产成本,需要在生胶或塑料胶中加入各种配合剂,如填充剂、补强剂、促进剂、硫化剂、防老剂、防焦剂等,这些配合剂有固体、液体等材料,将所加入的各种配合剂分散均匀,确保胶料的性质*致。
对混炼工艺的具体技术要求是:配合剂分散均匀,使配合剂.别是炭黑等补强性配合剂达到.好的分散度,以保证胶料性能*致。混炼后得到的混炼胶,其质量对进*步加工和制品质量有重要影响。若橡胶加工混炼不良,其胶料就会出现各种各样的问题,比如焦烧、喷霜等,使压延、压出、涂胶、硫化等工序难以正常进行,并导致成品性能下降。
橡胶的混炼过程包括四个阶段:混入、分散、混合、塑化。生胶或塑料胶在炼胶机中受到剪切和拉伸的作用产生流变和断裂、破碎,与配合剂充分接触,使其混入。这*过程称为润湿阶段或吃粉阶段。混入橡胶后的配合剂在机械力的作用下进*步被破碎成微小尺寸的细粒,同时增加接触面面积并进*步提高混合均匀性。所以又称微观分散。各种配合剂在生胶或塑炼胶中均匀分布的过程。所谓混合,是指仅增加配合剂在胶料中的分布均匀性,而不改变其粒子的尺寸大小,这*过程又称为宏观分散或简单混合。
混炼的质量是对胶料的进*步加工和成品的质量有着决定性的影响,混炼方法通常分为开炼机混炼和密炼机混炼两种。这两种方法都是间歇式混炼,这是目前.广泛的方法。混炼胶制备的*般工艺流程:配合剂补充加工→生胶及配合剂称量→混炼→质量检测。
混炼是将将橡胶(生胶)与各种配合剂在炼胶机内混合均匀的橡胶加工工艺。为了能够将粉状配合剂加入橡胶中,生胶须先经塑炼,提高其塑性及流动性。混炼过程是橡胶加工.基本的过程,加入配合剂后的混炼胶料的质量,对半成品的工艺性能和成品质量均具有决定性影响。橡胶混炼过程就其本质来说是配合剂在生胶中均匀分散的过程,粒状配合剂呈分散相,生胶呈连续相。在混炼过程中,橡胶分子结构、分子量大小及其分布、配合剂聚集状态均发生变化。通过混炼,橡胶与配合剂起了物理及化学作用,形成了新的结构。
2. 橡胶混炼配合剂的润湿分散性能
在橡胶行业中,由于生胶粘度很高,为了让各种配合剂均匀混合和分散,必须要使用炼胶机的强烈的机械作用来进行混合。这种炼胶机的功用类似干粉砂浆设备里面的混合机,主要用于进行均匀混合操作的。在操作过程中,使用各种配合剂,但由于其表面性质的区别,配合剂对于橡胶的活性也都不*致,按照表面.性,配合剂可以分为三种,*种是具有疏水性,如各种炭黑等。前者表面.性与生胶不同,因此不易被橡胶润湿;后者表面.性与生胶相近,易被橡胶润湿。为获得良好混炼效果,对亲水性配合剂的表面须加以化学改性,以提高它们与橡胶作用的活性,使用表面活性剂即可起到此种作用。另外*种是亲水性,如碳酸盐、陶土、氧化锌、锌钡白等;使用混炼的目的其实就是为了提高橡胶产品的使用性能,改进生产工艺以及降低生产成本,在这种要求下,必须使用各种配合剂,混炼不良,胶料会出现配合剂分散不均,胶料可塑度过低或过高、焦烧、喷霜等到现象,使后续工序难以正常进行,并且很可能还会导致成品橡胶产品性能下降。
粉粒状配合剂分散于橡胶中的难易程度与其表面性质有关。按照其表面性质基本上可分为两类:*类是具有亲水性,如碳酸盐、陶土、氧化锌、锌钡白、白炭黑、氧化镁及其他碱性无机物等;另*类是具有疏水性,如各种炭黑等。前者的表面性质与生胶不同,因而不易被润湿,后者表面性质与生胶相近,易被润湿。为了提高配合剂的分散程度,有效的办法是加入表面活性剂,表面活性剂大多为有机化合物,其中含有-OH、-NH2、-COOH、-NO2、-NO、-SH等.性基团,具有亲水性,另外他们分子结构中还含有非.性长链或苯环式烃基,具有疏水性。因而表面活性剂充当配合剂和橡胶之间的媒介的角色,提高了混炼效果,同时它还能稳定已分散的配合剂粒子在橡胶中的分散状态,从而提高混炼胶的稳定性。
加入分散剂后可明显缩短混炼时间,减少动力消耗,提高分散均匀性,产品硫化时不含有分散剂或内脱模剂的胶料,其流动性差,易出现废边过厚、尺寸超差及其产品缺胶等缺陷,污模粘模现象严重,都要经常清洗模具,制品光洁度差,启模取件困难,有时启模取件时产品被启破裂口,加入内脱模剂、分散剂后上述现象得到解决,.别是制品外观质量明显提高。
丁基橡胶混炼时配合剂分散困难,开炼机混炼时采用引料法(即待引料胶包辊后再加生胶和配合剂)或薄法——将配方中*半生胶以小辊矩反复薄通,待包辊后再加入另*半。用密炼机混炼时,装胶容量比天然橡胶大10﹪~20﹪,混炼温度在150℃为好,当填料多时也可采用两段混炼法和逆混炼法。乙丙橡胶混炼时不易发生过炼,配合剂分散均匀,但自粘性差。乙丙橡胶用开炼机混炼,*般先采用小辊矩使其连续包辊后,再逐步放宽辊矩,加入配合剂,辊温在60~70℃之间。采用密炼机混炼宜采用高温,混炼温度在150~160℃有助于填充剂和软化剂的分散及力学性能的提高。装胶容量可比其它胶料高10﹪~15﹪。氯磺化聚乙烯橡胶具有热塑性,加工中随着胶料温度上升,粘度迅速下降,该橡胶性能稳定,不易过炼。
炭黑分散到生胶或塑料胶的过程,先是橡胶渗入炭黑附聚体的空隙中,形成浓度很高的炭黑-橡胶聚集体团块,分散在不含炭黑的生胶或塑料胶中,然后这些炭黑-橡胶聚集体团块在足够大的物理剪切或拉伸力作用下被搓开,团块逐渐减小,逐渐混合,直到充分分散。在炭黑-橡胶聚集体团块中,炭黑形成的附集体,其内部存在着*种物理吸附的内聚力,只有受到大于这*物理吸附内聚力的物理剪切或拉伸力时才能将团块搓开。由于生胶或塑炼胶变形量所需的剪切或拉伸力与其粘度有关,要达到克服炭黑附聚体的物理内聚力将其搓开,要求生胶或塑炼胶有*定的粘度。随着分散过程的发展,炭黑包含的生胶或塑炼胶逐渐减少,胶料粘度逐渐下降。炭黑分散度和细粒子数目的提高,炭黑与生胶或塑炼胶之间接触面积增加,胶料的弹性恢复数值逐渐增大,当此值不再增加时,表明其分散过程*结。
天然橡胶具有良好的混炼性能,其包辊性好,在机械捏炼时,塑性增加快而生热量低,因此对配合剂的湿润性好,吃粉快,分散也较容易,混炼时间短,混炼操作易于掌握。但混炼时间过长时,会导致过炼,使硫化胶性能明显下降,严重时会产生粘辊现象。因此,混炼时应严格控制混炼时间等工艺条件。开炼机混炼时辊温*般控制在50~60℃(前辊应较后辊高5℃),液体软化剂的加入顺序要在填料之后,混炼时间*般为20~30min。密炼机混炼时,多采用-段混炼法,排胶温度*般控制在140℃以下。
3. 橡胶混炼前的准备
橡胶混炼前的准备工作主要包括:对原材料进行抽查、检验;对不适用的配合剂补充加工;配合剂的称量。原材料的质量检验通常对配合剂的检验内容主要有纯度、粒径、水分、机械杂质含量、灰分及挥发分含量、酸碱度以及液体配合剂的粘度等。具体依配合剂类型不同而异。生胶或塑炼胶除了检验其化学成分和门尼粘度外,还应该检验物理机械性能。
配合剂的补充加工主要有固体配合剂的粉碎;粉状配合剂的干燥和筛选;低熔点配合剂的预热融化和过滤;液体配合剂的加温和过滤;膏剂和母炼胶的制备等。块状或粗粒状配合剂需要经过粉碎、磨细处理或者刨成细片(如硬脂酸、石蜡、沥青和淞油等)才能使用,以便在胶料中分散。粉碎常用的设备有盘式粉碎机、球磨机、气流粉碎机、锤式破碎机、刨片机等。
当配合剂中含有较多水分或低挥发物杂质时,使得配合剂容易结团,不仅使筛选困难,而且在混炼时容易被压成大块凝聚物而不易分散,使得胶料或半成品硫化时内部容易产生气泡,造成废次品。所以需要除去或减少其中水分或低挥发物杂质。干燥设备有干燥室、真空干燥箱、螺旋式连续干燥机等。当配合剂的粒度及粒度分布达不到标准,或者其中含有机械杂质,如沙粒、木屑、小金属器件以及配合剂本身的大颗粒和结团等。因为这些杂质的混入,会降低硫化胶的物理机械性能,容易损坏设备。常用的设备有振动筛、鼓式选筛机、螺旋选筛机等。低熔点固体软化剂须先进行加热融化,达到脱水作用和降低粘度作用后,再趁热过滤去掉其中的各种机械杂质。而对粘度太高的液体软化剂,则应进行加温脱水并使其粘度减小,以便进行趁热过滤去掉杂质。
将个别的*些配合剂(短时间难以混炼均匀、生热量多、能耗大的)以比较大的比例事先与生胶或塑炼胶单.混合制成组分比较简单、高浓度的母炼胶。将某些配合剂,如促进剂、氧化锌、硫磺等,预先与液体软化剂混合制成膏状混合物,使得配合剂容易分散,降低粉状配合剂的飞扬,改善劳动条件。配合剂的称量是制备胶料前准备工作.主要的工序之*。
称量是否准确,对胶料的加工性能和产品质量都起着重要的作用。因此必须做到细致、不错不漏、准确无误。配合剂的称量和投料有两种方式:手工称量投料和自动称量投料。前者适用于技术程度不高的中小规模生产,后者适用于技术程度高的大规模生产。混炼可采用开炼机、密炼机和螺杆连续混炼机。用开炼机混炼时要求手工操作熟练,劳动强度大,且不安全。用密炼机混炼操作安全,劳动强度小,是目前应用.普遍的。
混炼要求配合剂均匀分散于生胶中,形成胶态分散体,以使硫化胶具有.*性能。同时对混炼胶料的可塑度也有*定要求,使之能符合后工序的要求。有*段和二段混炼法。前者是在橡胶中逐步添加配合剂。后者是先加入软化剂和粉末状填充剂进行.*阶段的粗混炼,胶料经冷却和放置*定时间后,再加硫黄和促进剂进行.二段混炼。
将橡胶(生胶)与各种配合剂在炼胶机内混合均匀的橡胶加工工艺。为了能够将粉状配合剂加入橡胶中,生胶须先经塑炼,提高其塑性及流动性。混炼过程是橡胶加工.基本的过程,加入配合剂后的混炼胶料的质量,对半成品的工艺性能和成品质量均具有决定性影响。
4. 橡胶混炼常用的设备
炼胶机是橡胶工厂用来制备混炼橡胶或对胶料进行热炼、塑炼、出型的*种辊筒外露的炼胶机械。橡胶混炼常用的设备主要有开炼机和密炼机两类。主要工作部件是两异向向内旋转的中空辊筒,装置在操作者*面的称作前辊,可通过手动或电动作水平前后移动,借以调节辊距,适应操作要求;后辊则是固定的,不能作前后移动。
开炼机是橡胶制品生产厂应用比较早的*种混炼橡胶设备。在压延机生产线上,开炼机在压延机前、混合机后,作用是把混合均匀的原料进行混炼、塑化,为压延机压延成型橡胶制品提*混合炼胶较均匀的熔融料。
密炼机混炼与开炼机混炼相比,具有混炼时间短、效率高、机械化自动化程度高、胶料质量好、劳动强度低、操作安全、药品飞扬损失小、环境卫生条件好等优点,但密炼机混炼室散热困难,混炼温度高且难以控制,使对温度敏感的胶料受到限制,不适于浅色胶料和品种变换频繁的胶料混炼;另外密炼机混炼还需配备相应的下片装置。密炼机通过转子、上下.栓在密炼室中产生复杂的流动方式和高剪切力,使橡胶配合剂和粒状添加剂很快粉碎和均匀分散,是*种高效的混炼方法。
5. 橡胶混炼的过程和混炼方法
橡胶在开放式炼胶机两个旋转辊筒的间隙中,反复受到剪切作用,靠手工操作控制。主要包括三个阶段:
生胶加热。即将已塑炼的生胶在机上再次重炼,加热软化,并加入其他聚合物共混;
加配合剂。*般先加软化剂、硬脂酸等,然后加入粉料和炭黑等(炭黑也可预先和部分生胶先单.混为母炼胶)。硫磺*般在混炼的.后或在胶料经停放,于.二次重炼时再加入;
当所有配合剂添加完毕后,应再继续翻炼,使混合均匀,然后卸下胶片。
开炼机混炼有*段混炼和分段混炼两种工艺方法。无论是*段混炼还是两段混炼,在混炼操作时,都先沿大牙轮*侧加入生胶、母炼胶或并用胶,然后依据配方加入各种配合剂进行混炼。密闭式炼胶机混炼过程:密闭式炼胶机的转子表面和混炼室壁面之间的间隙大小,随转子转动有很大范围的变化,对胶料产生强烈的剪切作用。混炼效果比开放式炼胶机大得多,各种粉料配合剂在混炼室内和胶料混合而不飞扬在外,而且自动仪表控制混炼过程,例如在混炼过程中,胶料温度、物料在室内的体积和所耗电功率的变化有*定规律。
密炼机通过转子、上下.栓在密炼室中产生复杂的流动方式和高剪切力,使橡胶配合剂和粒状添加剂很快粉碎和均匀分散,是*种高效的混炼方法。但是高剪切力会使物料温度在混炼中迅速上升,*般会达到130℃。这已超过了大多数硫化系统的活化温度,会使胶料发生早期硫化(焦烧)。*般的做法是将大部分物料在密炼机中混炼,然后将胶料从密炼机排放到开炼机上,在开炼机上加硫化剂或超速促进剂。由于开炼机实际上只在辊缝线上对胶料有挤压作用,而提*了很大的冷却面积,致物料的温度降低。在这*阶段加入硫化剂可以避免胶料发生早期硫化(焦烧)。
密炼机混炼分为湿润、分散和涅炼,密炼机混炼石在高温加压下进行的。开炼机的混合过程分为三个阶段,即包辊(加入生胶的软化阶段)、吃粉(加入粉剂的混合阶段)和翻炼(吃粉后使生胶和配合剂均达到均匀分散的阶段)。开炼机混胶依胶料种类、用途、性能要求不同,工艺条件也不同。混炼中要注意加胶量、加料顺序、辊距、辊温、混炼时间、辊筒的转速和速比等各种因素。既不能混炼不足,又不能过炼。
密炼机混炼操作方法主要有*段混炼法、二段混炼法、引料法和逆混法:
*段混炼法是指经密炼机和压片机*次完成混炼,然后压片得混炼胶的方法。在*段混炼操作中,常采用分批逐步加料法,为使胶料不*于剧烈升高,*般采用慢速密炼机,也可以采用双速密炼机。其加料顺序为生胶—小料—补强剂—填充剂—油类软化剂—排料—冷却—加硫磺及超促进剂。胶料直接排入压片机,薄通数次后,使胶料降*100℃以下,再加入硫黄和超促进剂,翻炼均匀后下片冷却。此法的优点是比二段混炼法的胶料停放时间短和占地面积小,其缺点是胶料可塑性偏低,填充补强剂不易分散均匀,而且胶料在密炼机中的炼胶时间长,易产生早期硫化。此法较适用于天然橡胶胶料和合成橡胶比例不超过50%的胶料。
密炼机*段混炼法从加料、混合到下片冷却*次完成。*般要和压片机配合使用,先把生胶或塑炼胶和配合剂按*定顺序投入密炼机的混炼室内,混匀后排胶于压片机上压片,并使胶料温度降低,此时再加入硫化剂和需低温加入的配合剂,再通过捣胶装置或人工捣胶反复压炼,以混炼均匀,经密炼机和压片机*次混炼得到均匀的混炼胶的方法叫做*段混炼法。
两段混炼法是指两次通过密炼机混炼压片制成混炼胶的方法。这种方法适用于合成橡胶含量超过50%得胶料,可以避免*段混炼法过程中混炼时间长、胶料温度高的缺点。.*阶段混炼与*段混炼法*样,只是不加硫化和活性大的促进剂,*段混炼完后下片冷却,停放*定的时间,然后再进行.二段混炼。混炼均匀后排料到压片机上再加硫化剂,翻炼后下片。分段混炼法每次炼胶时间较短,混炼温度较低,配合剂分散更均匀,胶料质量高。
6. 橡胶加工混炼的工艺方法及操作.点
混炼是橡胶加工工艺过程中.为重要*个组成部分之*,混炼可分开炼机、密炼机混炼。密炼机混炼还分高温低温之分,不同的设备、配方、硫化工艺、生产环境其混炼工艺也应该是不尽相同的。开炼混炼与密炼混炼各有不同的优缺点,开炼混炼存在着污染、分散不均、高溶点物质更难分散等不良因素,相对来说是低温混炼,所以开炼混炼工艺后,需停放,使配合剂进*步扩散,在*般情况下是必须的,同时可以利用其低温混炼的.点可以将包括超速促进剂在内的小药同时*起加入混炼,所以开炼混炼的胶料有时其硫化T90比密炼加工的更加稳定。
密炼工艺的方法有多种多样,其.重要的环节还是温度、时间、压力三方面的综合控制。温度控制是.为重要的*关,混炼温度可分为高温、中温、低温三种方法、高温混炼*般在130~150℃之间,其混炼工艺上是不能加入任何促进剂或硫化剂,*般适用于高速密炼机,如轮胎胶料中的用SI69偶联白炭黑,其密炼温度达到了150℃,并严格控制密炼时间。
中温混炼*般温度控制在110~135℃不等,不同的配方、工艺可以选择不同的排胶温度。实际上大多数中小型企业都是选择这个阶段的混炼温度,在这个混炼温度阶段操作有几个.点:*是高溶点树脂、投料袋等可以充分溶化有利于分散;二是*般温度上升到这个阶段大部分胶料已经混炼均匀可以排胶;三是在这个阶段混炼是可以加入临界活化温度较高的促进剂品种*起混炼将有利于分散;四是胶料的门尼粘度容易控制。采用低温混炼方的工厂也较多,可以使用与开炼混炼相同的加料程序。低温混炼*般使用在较易混炼的、充油量较多的、补强剂结构较低的配合体系中。混炼工艺是*段较为重要的加工过程,混炼质量的优劣不但直接影响胶料的物理性能,而且还不能确保胶料的正常的门尼粘度,从而还会影响后段的硫化加工工艺及硫化速度。
橡胶密炼机自十九世纪初发明以来,*直作为橡胶工业生产中的关键设备而投入使用。当下汽车行业的快速发展,带动了橡胶轮胎市场需求量的增加,在全球提倡环保节能的大环境下,橡胶密炼机也开始向着环保节能的大方向发展,而大容量密炼机产品的出现也顺应了这样的发展趋势。